The quality of a paint job depends not only on the technique used, but also on the environment in which it's performed. Small impurities in the air can compromise the finish, especially in sectors that require high precision. This is where pressurization modules come into play, acting as essential allies in ensuring a controlled, contaminant-free environment.
But what are pressurization modules, and how do they work? These devices filter the air entering the paint booth using filtration barriers and a positive pressure system, creating an ideal environment for high-quality paint finishes.
In this article, we'll explore the benefits of pressurizing modules, from worker protection to improved finish quality, as well as practical tips on how to choose the ideal pressurizing module for your project, ensuring efficiency, safety, and impeccable results.
What are pressurizer modules?
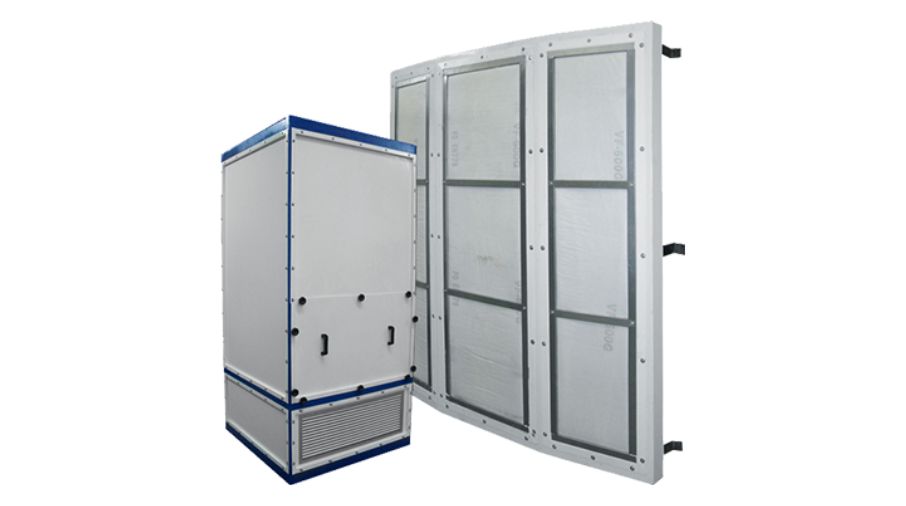
Pressurization modules are equipment used in paint booths to ensure a controlled, contaminant-free environment during the painting process. They filter the air entering the booth and maintain a positive pressure inside. This means the volume of filtered air entering the booth is greater than the intake air, preventing the entry of unfiltered outside air, which could introduce impurities and compromise paint quality.
The general operation of a positive pressure module is very simple. Initially, the pressure module injects a continuous flow of filtered air into the environment, generating a slight overpressure, which prevents contaminant particles from entering through cracks or openings.
This way, the system maintains a constant exchange of air, reducing the concentration of dust, chemical vapors, and microorganisms. Furthermore, the clean air is strategically distributed to avoid uneven surfaces and ensure that critical areas receive maximum protection.
The main components of the pressurizing modules include:
Air filters: Filters are essential components of a pressurizer module. Pre-filters capture larger particles—such as dust and soot—extending the lifespan of finer filters. High-efficiency filters (HEPA or activated carbon) eliminate microparticles, pollutants, and even chemical odors from the air. However, periodic replacement is essential to maintain filtration efficiency.
Fans and motors: Fans and motors are responsible for pushing filtered air into the environment and need to be sized correctly to ensure a constant and adequate flow of air.
Control and monitoring systems: Finally, control systems, such as pressure control, automatically adjust airflow to maintain positive pressure. Electronic control panels allow you to adjust ventilation intensity and alert you to the need for filter maintenance. Other indicators warn of pressure loss or filter saturation.
Benefits of pressurizing modules
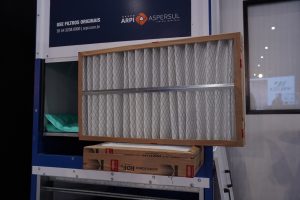
The use of pressurizing modules brings enormous benefits to painting and finishing projects. Let's take a look at the main ones:
Prevention of impurities and particles in paintwork
The positive pressure generated by the pressurizing module creates a barrier against contaminants, preventing the entry of dust, soot, paint residue, and other unwanted particles. This creates a controlled environment, preventing airborne dirt from sticking to the painted surface (which can compromise adhesion and finish), and ensuring a high quality standard—essential for automotive and aeronautical paint industries—where any impurity can compromise the aesthetics and durability of the coating.
Improved finish quality and durability
The absence of impurities results in a smoother, more uniform surface—i.e., a homogeneous paint job, free from bubbles, marks, or imperfections. This characteristic also influences better paint adhesion, as application in a contaminant-free environment allows the paint to adhere properly, increasing the durability of the coating and reducing problems such as peeling, staining, or discoloration due to contaminants.
Reduction of rework and costs
Because painting is done under ideal conditions, there's less need for touch-ups and reapplications, meaning less wasted materials. This also saves time, as it reduces the need for sanding, polishing, and re-applications due to defects caused by dust and dirt. Another important point is that the efficiency of the pressurized system prevents overloading fans and filtration equipment, resulting in energy savings.
Increased efficiency and productivity
Filtered air keeps the area free of impurities, allowing operators to work uninterrupted for corrections in a stable and predictable environment. This speeds up the entire painting process, as the absence of particles that cause defects allows the paint to dry properly, reducing the time between steps and improving standardization. This means that part quality remains consistent regardless of production volume.
Ensuring a cleaner and safer work environment
Another benefit of using pressurizing modules is that they reduce the inhalation of harmful particles, as filtered air reduces workers' exposure to dust, chemical vapors, and solvents, reducing health risks. Furthermore, the modules also help companies comply with environmental and safety standards, more easily meeting air quality and occupational safety regulations.
How to choose the ideal pressurizing module
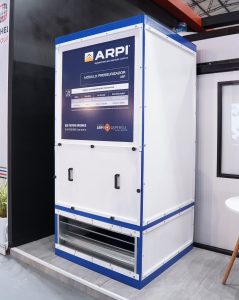
Below we will list the main factors to consider when choosing your ideal pressurizing module:
Size and type of paint booth
Small or individual booths require compact modules with airflows adjusted to tight spaces, unlike medium-sized or industrial booths, which require more powerful modules capable of maintaining positive pressure in larger areas. Open or semi-open booths, on the other hand, require pressurizing modules with greater airflow control, as there is a greater risk of external contaminants entering. Choosing an undersized module can result in insufficient pressure, while an oversized one can unnecessarily increase energy consumption.
Required air flow
Calculating the ideal flow rate should take into account the booth volume to ensure efficient air exchange, with the recommended rate varying according to the booth size and the type of painting performed. Therefore, the module must maintain a constant flow of filtered air to avoid fluctuations that could compromise paint quality and avoid wasted energy and operating costs.
Ease of installation and maintenance
Modular models are easier to install and integrate with different types of paint booths, but it's important to consider the booth's design. Quick access to filters and other components allows for simplified maintenance and reduces downtime. Similarly, choose brands with efficient technical support and readily available spare parts.
If you're looking for excellent painting with a flawless, impurity-free finish, pressurized modules are the ideal solution. For projects that demand high standards, trust the expertise of Aspersul, a leader in painting solutions with over 25 years of experience. Visit our website or speak to one of our experts.
Did you like this post? Share it with your friends or on social media. For more tips on painting and its equipment, visit our blog, always with exclusive content.